製造技術力と分析力で
お客様のニーズにお応えします
高性能のマルチプラントを複数保有する高松工場は、塩素化反応の技術をベースに多種多様な化学製品を製造しています。
数十キロの試作段階から、小規模・中規模生産、数百トンの量産まで、お客様のニーズに応じて多様な形態での受託が可能です。
高松工場の3つの特徴
-
特異な技術
塩素ガスを用いる塩素化をベースに、技術展開しています。
-
特有の設備
高温反応缶、高粘度・高圧対応反応缶、超音波分散装置、塩素タンク、危険物冷凍倉庫など特長ある設備を保有しています。
-
少量生産から量産まで対応
受託規模は数十キロ単位から数百トン単位まで、無機、有機、高分子、分野を問わず対応可能です。
高松工場 施設地図
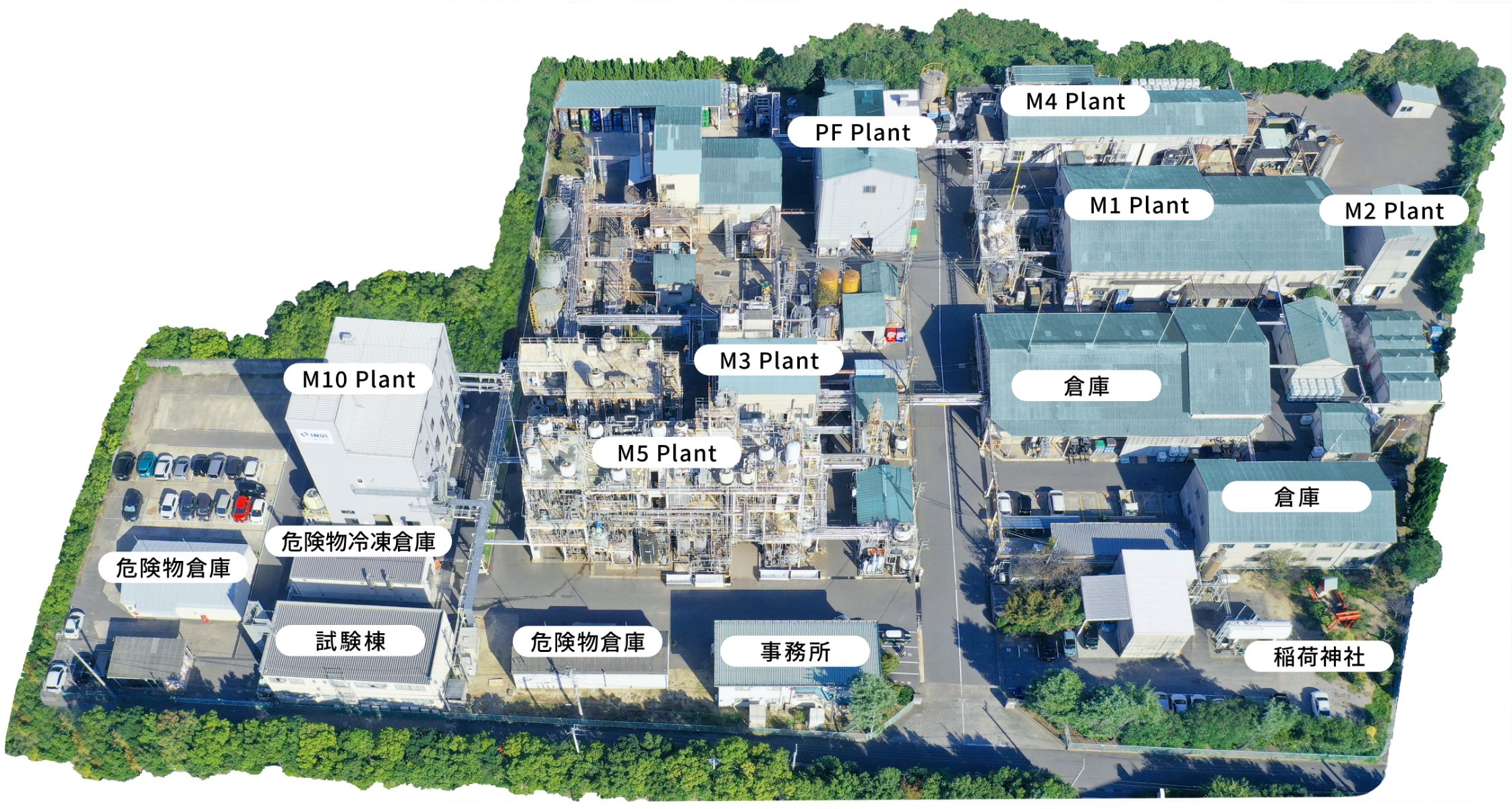
プラント紹介
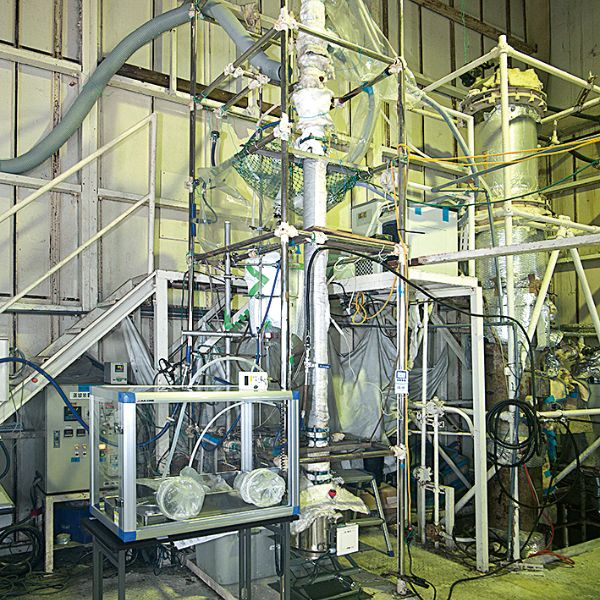
数百リットルスケールのガラス製装置を主体とした反応 · 蒸留装置。生産方法を検証するための試験的生産を行う設備です。
設備 | 容量 | 材質 | 温度(℃) | 圧力(kPa) | 備考 |
---|---|---|---|---|---|
反応槽 | 500L | GL×ガラス | −10〜150 | ||
蒸留缶 | 10L | ガラス×SUS316L | 常温~200 | 0.1 | 蒸留段数30段 |
蒸留缶 | 160L | ガラス×ガラス | 常温〜180 | 0.7 | 蒸留段数5段 |
蒸留缶 | 500L | GL×ガラス | 常温~170 | 0.7 | 蒸留段数3段 |
反応槽 | 500L | SUS304 | 常温~150 |
注意:充填塔のある反応槽・蒸留缶の材質欄の表記は「蒸留缶材質」×「充填物材質」
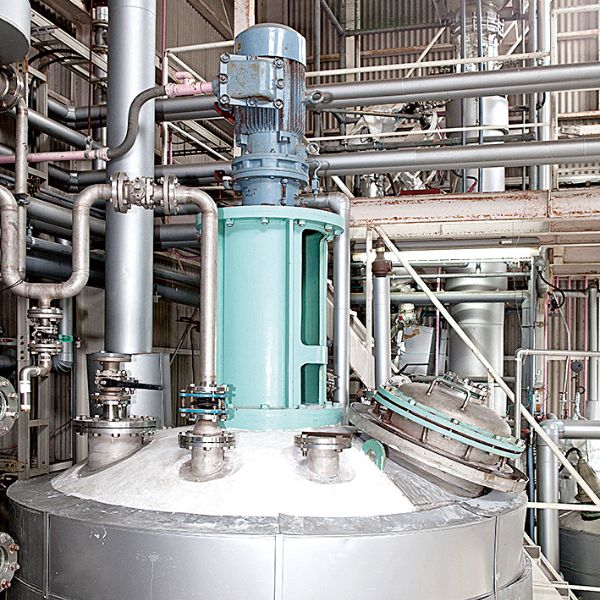
2,000〜5,000リットルのGL及びSUSの装置をそろえた生産設備です。
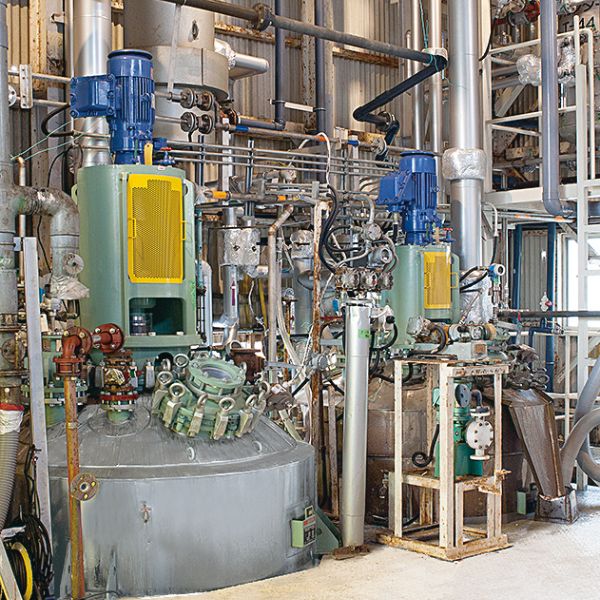
2,500~4,000リットルGL製反応・蒸留装置と4,000リットルSUS精留装置を備えており、腐食性の高温反応等、各種化学反応に対応できます。
設備 | 容量 | 材質 | 温度(℃) | 圧力(kPa) | 備考 |
---|---|---|---|---|---|
反応槽 | 3000L | GL | 常温~200 | ベンドリ ーフ翼 | |
反応槽 | 4000L | GL | −10〜150 | ||
反応槽 | 4000L | GL | −10〜150 | フルゾーン翼 | |
蒸留缶 | 2500L | GLx 磁製 | 常温~170 | 1 | 蒸留段数3段 |
蒸留缶 | 4000L | SUS316 | 常温〜250 | 1 | 蒸留段数15段 |
スクリュー デカンタ |
450L/h | SUS304 |
注意:充填塔のある反応槽・蒸留缶の材質欄の表記は「蒸留缶材質」×「充填物材質」
200〜500Lの小型装置をそろえた生産設備です。
設備 | 容量 | 材質 | 温度(℃) | 圧力(kPa) | 備考 |
---|---|---|---|---|---|
反応槽 | 200L | GL | 10〜120 | ||
反応槽 | 200L | SUS316 | −10〜150 | ||
反応槽 | 500L | GL | −10〜150 | ||
反応槽 | 500L | GL | −10〜150 |
注意:充填塔のある反応槽・蒸留缶の材質欄の表記は「蒸留缶材質」×「充填物材質」
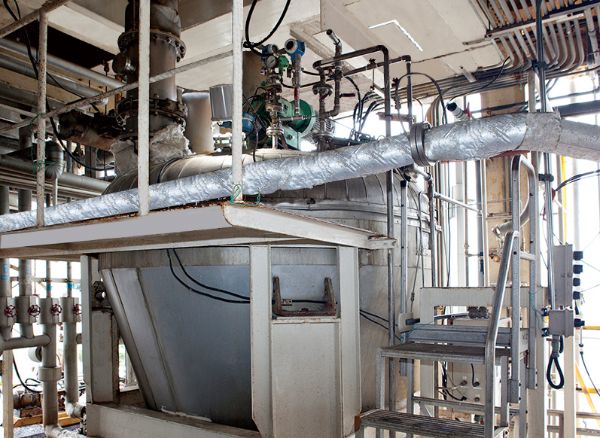
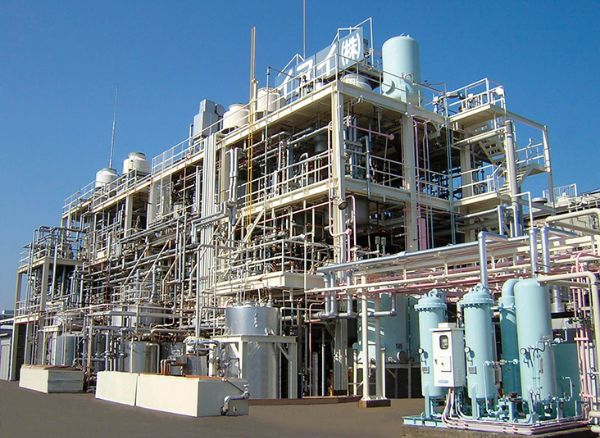
1,000〜10,000リットルスケールの各種装置を擁する本格的製造設備。塩素化· 高温反応装置・耐腐食性反応蒸留装置・粉体処理装置・40段精留装置等を備えています。
設備 | 機器No. | 容量 | 材質 | 温度(℃) | 圧力 (kPa) |
備考 |
---|---|---|---|---|---|---|
反応槽 | R-111 | 1000L | GL | 10~150 | ||
反応槽 | R-112 | 1000L | GL | 10~150 | ||
反応槽 | R-113 | 2500L | GL | 10~140 | ||
反応槽 | R-114 | 2500L | GL | 10~140 | ||
反応槽 | R-102 | 3000L | GL | −10~150 | ||
反応槽 | R-801 | 3000L | GLx 磁製 | 10~140 | 1.3 | 蒸留段数5段 |
反応槽 | R-101 | 6000L | GL | −10~150 | ||
反応槽 | R-811 | 6000L | SUS316 | −10~170 | 1.3 | |
反応槽 | R-851 | 6000L | SUS316 | 常温~140 | ||
反応槽 | R-843 | 7000L | SUS304 | 常温~80 | ||
反応槽 | R-822 | 8000L | GL | 10~140 | ||
反応槽 | R-841 | 8000L | GL | 常温~140 | 1.3 | ベンドリーフ翼 |
反応槽 | D-201 | 8000L | GLx 磁製 | 常温~190 | 1 | 蒸留段数5段 |
反応槽 | R-856 | 8000L | SUS316xSUS304 | 常温~250 | 蒸留段数7.5段 | |
反応槽 | R-842 | 10000L | GL | 常温~120 | ||
反応槽 | R-821 | 10000L | SUS316 | −10~140 | 1.3 | |
蒸留缶 | D-301 | 7000L | SUS316LxSUS316L | 常温~190 | 1.3 | 蒸留段数40段 |
遠心分離器 | F-822 | 40インチ | SUS304 | |||
遠心分離器 | F-852 | 42インチ | SUS316 | |||
真空乾燥機 | K-852 | 3000L | SUS304 | 常温~120 | 1.3 | |
他 受槽貯槽 |
注意:充填塔のある反応槽・蒸留缶の材質欄の表記は「蒸留缶材質」×「充填物材質」

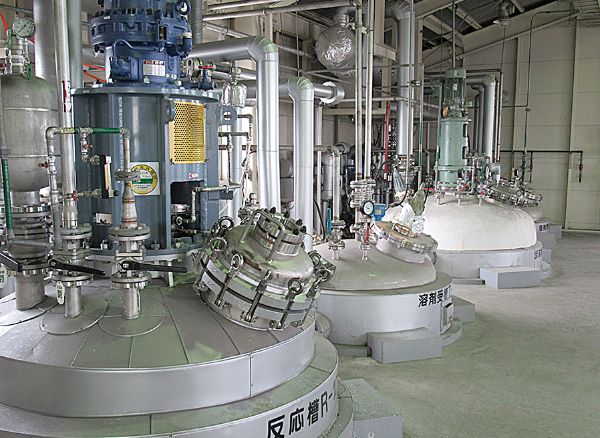
3,000 リットルSUS 圧力釜を備えた粉体専用設備。揮発性溶剤を含んだ粉体の取扱いが可能です。
設備 | 機器No. | 容量 | 材質 | 温度(℃) | 圧力 (kPa) |
備考 |
---|---|---|---|---|---|---|
反応槽 | R-10 | 3000L | SUS316L | 常温~180 | 一圧容器0.6MPa マックスブレンド翼 |
|
反応槽 | R-20 | 6000L | SUS304 | 常温~150 | ||
晶析槽 | R-30 | 6000L | SUS304 | 常温~150 | ||
蒸留缶 | D-40 | 6000L | SUS316L× SUS316L |
常温~170 | 1.3 | 蒸留段数20段 |
遠心分離器 | CF-10 | 36インチ | SUS304 | |||
遠心分離器 | CF-20 | 42インチ | SUS304 | |||
真空乾燥機 | DR-70 | 4000L | SUS316 | 常温~120 | 1 | |
真空乾燥機 | DR-75 | 3000L | SUS304 | 常温~120 | 1 | |
他 受槽貯槽 |
注意:充填塔のある反応槽・蒸留缶の材質欄の表記は「蒸留缶材質」×「充填物材質」
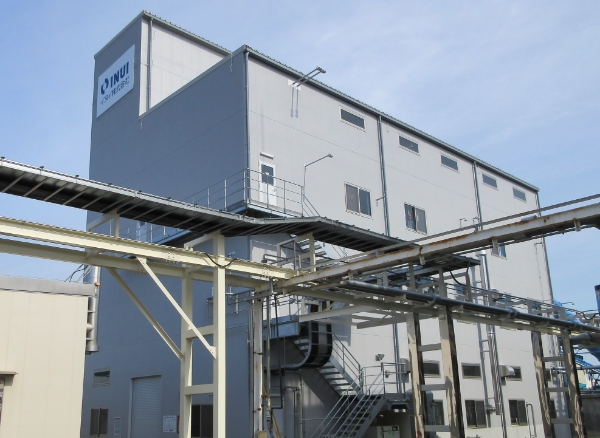
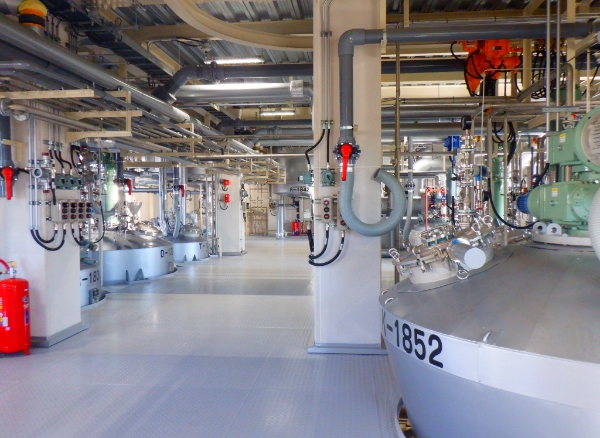
4,000~10,000リットルスケールの各種装置を擁する本格的製造設備。
加圧・高温反応装置、粉体処理装置・40段精留装置等を備えています。
設備 | 機器No. | 容量 | 材質 | 温度(℃) | 圧力 (kPa) |
備考 |
---|---|---|---|---|---|---|
反応槽 | R-1801 | 4000L | GL×セラミック | 10~140 | 2 | 蒸留段数 6段 |
反応槽 | R-1811 | 7000L | SUS316 | -10~165 | 2 | 一圧容器 0.6MPa |
反応槽 | R-1821 | 10000L | SUS316 | 10~130 | ||
反応槽 | R-1841 | 8000L | GL | 10~120 | フルゾーン翼 | |
反応槽 | R-1842 | 8000L | GL | 10~120 | ||
反応槽 | R-1851 | 6000L | SUS316 | 10~120 | ||
反応槽 | D-1201 | 8000L | SUS316L× SUS316L |
常温~230 | 2 | 蒸留段数 10段 |
蒸留槽 | D-1301 | 7000L | SUS316L× SUS316L |
常温~230 | 2 | 蒸留段数 40段 |
遠心分離機 | F-1852 | 42インチ | SUS316 | |||
乾燥機 | K-1852 | 3000L | SUS316 | 常温~120 | 2 | |
他 受槽貯槽 |
注意:充填塔のある反応槽・蒸留缶の材質欄の表記は「蒸留缶材質」×「充填物材質」
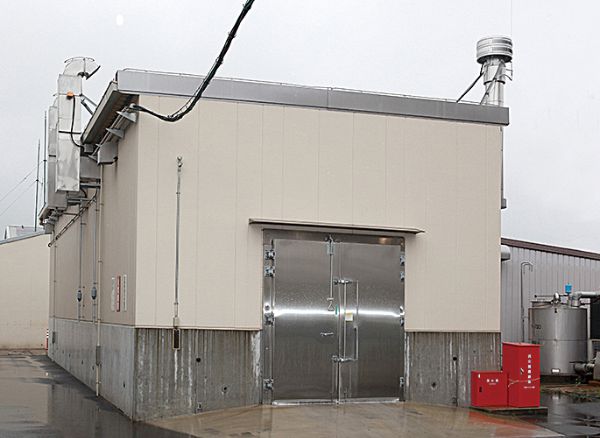
- 危険物冷凍倉庫
- 超音波分散装置
- 加圧・減圧単板ろ過機(SUS 500~1,000φ)
- コニカルドライヤー(GL-1000L、SUS-1500L)
- 塩素化装置(特定高圧ガス消費施設)
- 窒素発生装置
- イオン交換水製造設備
- 廃水処理設備
分析機器
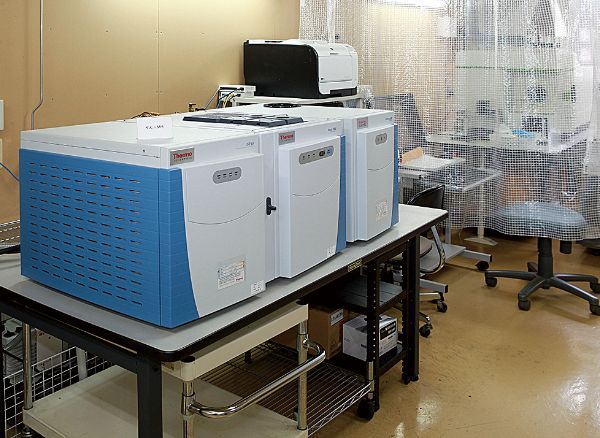
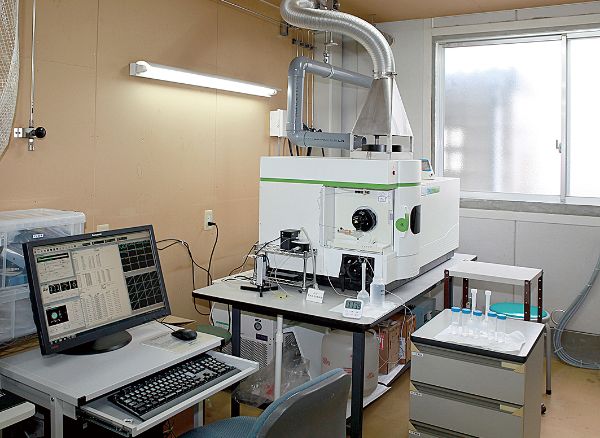
分析機器リスト
装置 | 仕様 |
---|---|
ガスクロマトグラフィー | FID、TCD検出器 |
ガスクロマトグラフ質量分析計 | 直接導入法、ヘッドスペース法 |
高速液体クロマトグラフィー | UV-VIS、PDA、RI、蛍光検出器 |
ゲル浸透クロマトグラフィー | RI検出器 |
イオンクロマトグラフィー | 陰イオン |
ICP発光分析装置 | |
示差熱・熱重量同時測定装置 (TG-DTA) |
|
示差走査熱量計(DSC) | |
赤外分光光度計 | |
紫外可視分光光度計 | |
X線回折装置 | |
レーザー回折・散乱式粒子径分布測定装置 | |
動的光散乱式粒度分布測定装置 | |
カールフィッシャー水分計 | 容量法、電量法 |
粘度計 | E型、BM型 |
溶融粘度計 | |
自動融点測定装置 | |
自動滴定装置 |
高松工場の沿革
イヌイの製造部門は、明治時代末期に製塩業の副産物である苦汁から塩化マグネシウム・炭酸マグネシウムを製造する目的で開設されました。
その後、大正8年に高松市築港東海岸に工場を移転。昭和45年には、高松市香西本町に高松第二工場を建設し、これが現在の高松工場となっています。
1911年 (明治44年) |
高松製薬所開設 |
---|---|
1919年 (大正8年) |
高松市築港東海岸に高松製薬所を移転 |
1936年 (昭和11年) |
臭素、硫酸マグネシウムの生産を開始 |
1947年 (昭和22年) |
局方塩の製造を開始 |
1951年 (昭和26年) |
臭素、ブロム酸カリの生産を開始 |
1953年 (昭和28年) |
農薬加工を開始 |
1959年 (昭和34年) |
モノクロルフェノールの生産を開始 |
1970年 (昭和45年) |
高松市香西本町に高松第二工場を建設 |
1980年 (昭和55年) |
M-1プラントを建設 |
1984年 (昭和59年) |
M-2プラントを建設 |
1987年 (昭和62年) |
M-3プラントを建設 |
1990年 (平成2年) |
医薬品中間体の生産設備として、M-5プラントを建設 |
1996年 (平成8年) |
M-8プラントを建設 |
1999年 (平成11年) |
M-5プラントを増設(一次) |
2001年 (平成13年) |
M-5プラントを増設(二次) 高松工場(高松市築港)に残っていた一部の生産設備を高松第二工場へ移転し、生産拠点を統合 |
2002年 (平成14年) |
試験棟建設 |
2007年 (平成19年) |
PF(粉体)プラントを建設 |
2008年 (平成20年) |
M-5プラントを増設(三次) |
2017年 (平成29年) |
エコステージ1 認証取得(高松工場の環境方針PDF) |
2024年 (令和6年) |
M-10プラントを建設 |